I'm back from the Hill Country Spinning Retreat at
Mo Ranch. When I first heard about it on Ravelry, I took a big leap of faith and signed up immediately. There's no way I was going to pass on a week of spinning and dyeing instruction with the inspirational
Judith MacKenzie McCuin, and in the Texas hill country! I could drive and take everything I could pack in the car. Was I really sending a big check to someone I didn't know, to attend a retreat with a group of strangers I was meeting on the internet? You betcha! Thankfully Roddie decided to go too, so I knew I wouldn't totally be alone. Turned out that I would know two other people, and made 20 new friends. Be prepared, this is going to be a REALLY long post with LOTS of photos! Here are Roddie and I arriving and meeting our hostess and workshop organizer, Karen.

Mo Ranch is a beautiful, Presbyterian retreat facility near Hunt, Texas. We had the entire Guest Lodge to ourselved for the week. In addition to the guest rooms, we had access to a full kitchen, dining room, sitting area with a gorgeous fireplace, and huge meeting room. It was the perfect location for a workshop where each participant had a LOT of "stuff" besides their spinning wheel.
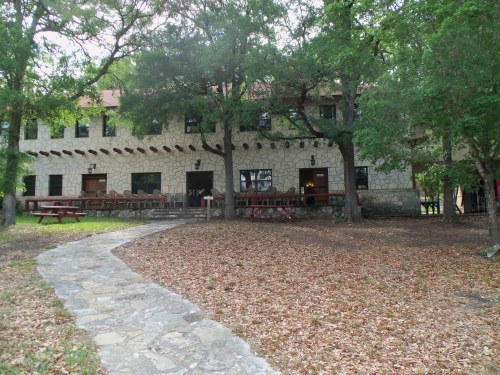
Our view of the river from the patio
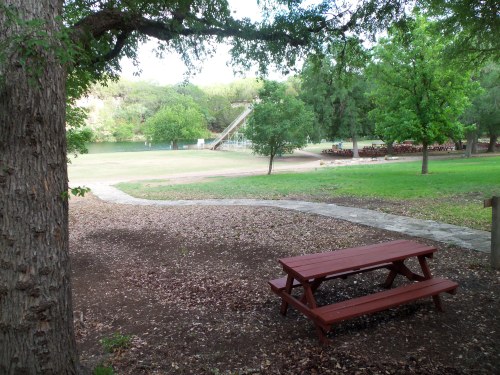
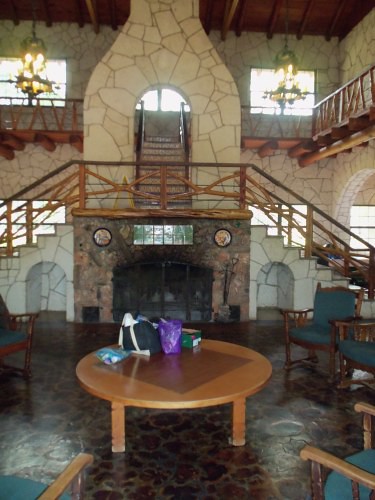
There was even an area off to the side of the meeting room where fiber vendors set up tables so that we could get a shopping fix any time we pleased. We spent quite a bit of time fondling the wares by
Alecia Goes Around,
Hill Country Weavers,
Yarnorama, and
Kai Ranch Mohair.
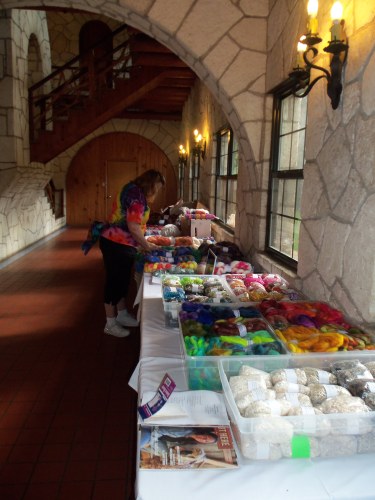
Cecil and Darlene from
Buffalo Gold came out and brought samples for us to spin, as well as a great selection of their luxury yarns and fibers for purchase.
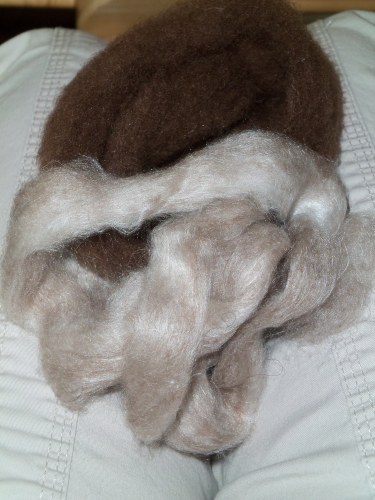
Judith even brought some of her hand-dyed
Buffalo Gals yarn. I snagged some beautiful deep turquoise/green!
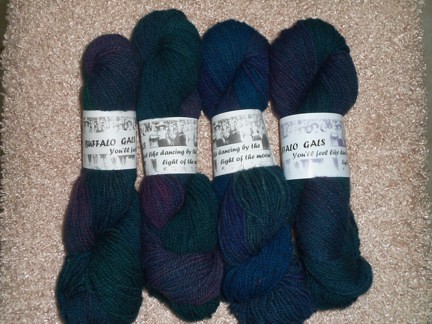
_____________________________________________________________
We began the week with a study of color. Judith made a big circle of Coopworth roving dyed in various colorways.
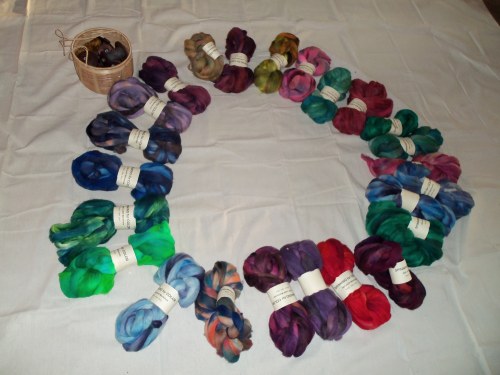
We drew numbers, then each person picked one. Then we divided that into quarters and traded two of them with other people. Since I was toward the end of the choices, I started with a sort of seafoam green roving (which was atrocious!) and added burgundy and dark blue to try and improve it.
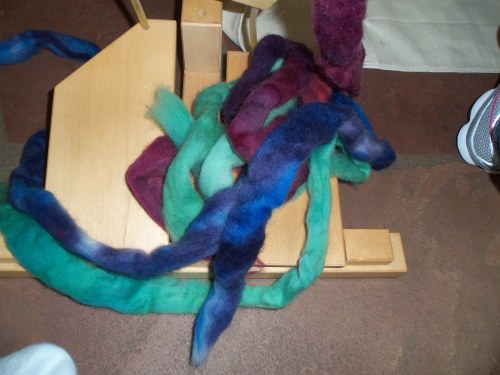
After spinning all the roving, it was finished into a 2-ply yarn. Still totally disliking the colors, I nicknamed my colorway "butt ugly". It's really funny how certain colors speak to you, and others are so repulsive. In this case, the green and blue worked pretty well together, but the burgundy was so disharmonious that it just screamed at you. Next I knitted a small swatch in garter stitch, which improved it a little. But since it was a 2-ply worsted spun yarn it felt very coarse, with the stitches pulling away from each other rather than melding together.
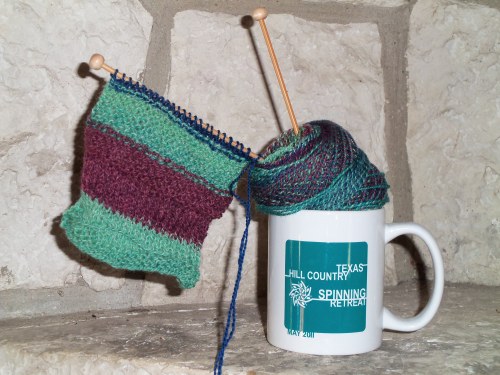
Since 2-ply works very well as a weaving yarn, we warped Cora's rigid heddle loom with turquoise perle cotton to see what happened to the colors. This was the most successful option, but the burgundy was still not quite working.
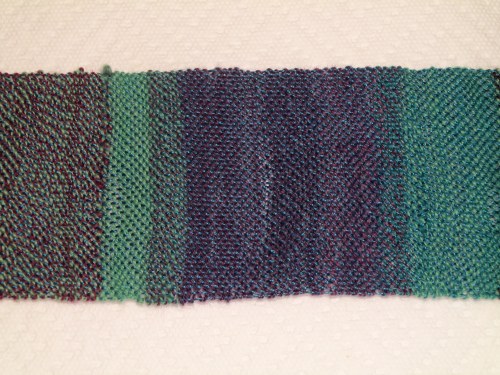
Thursday was dye day, so I decided to try overdying the finished yarn with blue. This gave all three colors a common tone which balanced things out much better. Here's the overdyed ball with the original fiber, yarn, knitted and woven.
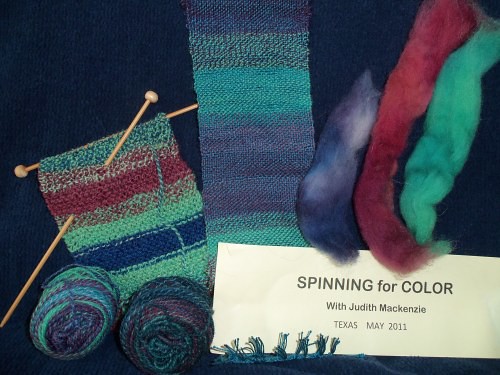
_____________________________________________________________
Our next color adventure began on Wednesday. Judith circled the floor with big bumps of Ashland Bay merino top in a huge rainbow of colors. This is wonderfully yummy stuff to work with!
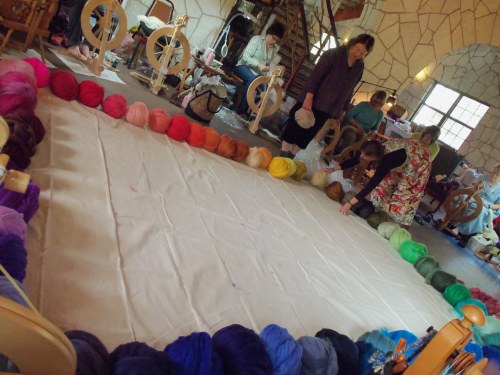
Our task was to choose five colors and spin a cabled sock weight yarn. It takes about 3oz of fiber for a pair of socks, so this was going to start at the ranch and end up being homework.
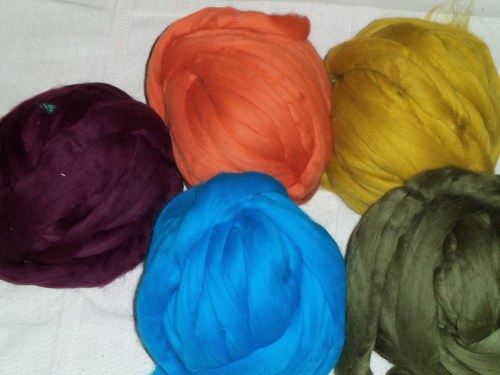
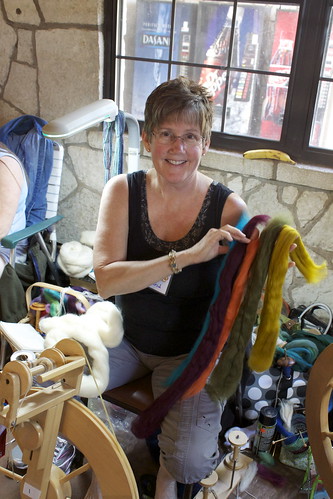
This was going to be a marled yarn, which meant that we had to alternate the colors throughout the singles. Judith made it look so easy to hold onto three colors at a time and just spin back and forth, but for many of the rest of us we ended up doing a lot of starting and stopping to change colors. Maybe after I've been spinning 60 years, I'll be adept at it too!
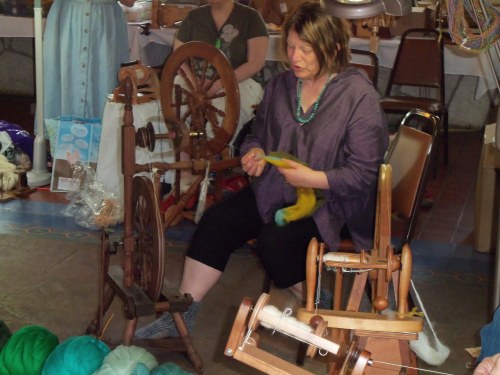
To create a cabled yarn, you have to spin your singles, over ply them so that they have a lot of energy, then ply those together again in the opposite direction. That's a lot of spinning! So here are the singles...
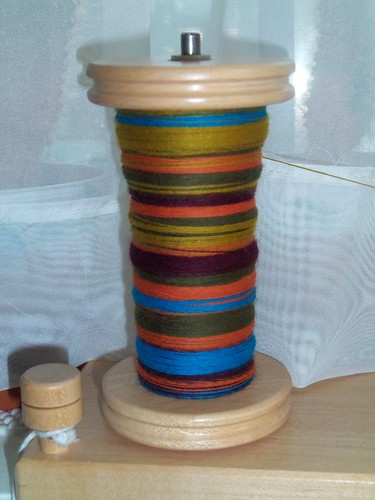
2-ply...
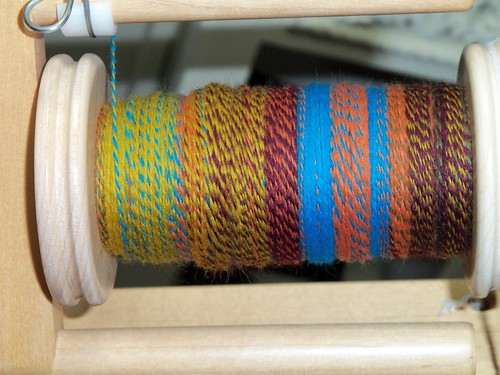
and the finished cabled yarn with a knitted swatch...

All that's left to do is to knit it into a pair of socks for next year's workshop!
_____________________________________________________________
On Thursday, we began learning about dyeing. Judith has her own set of colors she uses (and sells in a kit!) which consist of the primes: cyan, magenta, yellow, plus the modifier colors: worker blue, worker red, violet, orange, brown, and black. From these she can create just about anything.
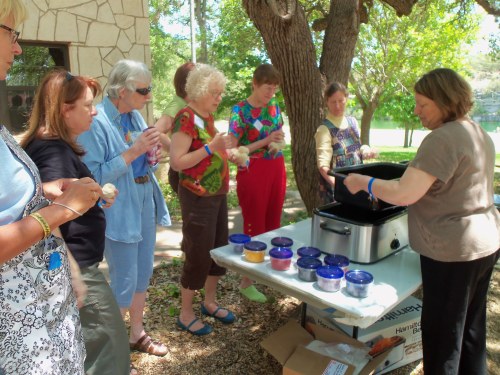
We started out by spinning singles of undyed merino top using a semi-worsted technique. These balls were then loaded into the roaster, ready for Judith to demonstrate how the colors react with each other.
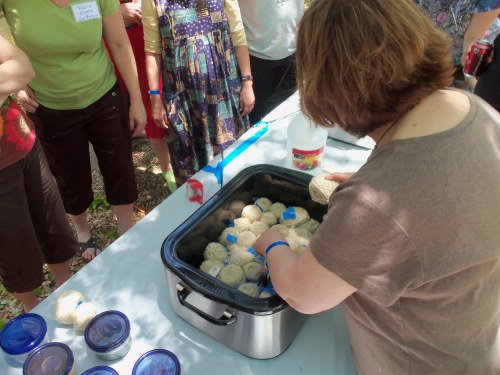
Next comes a big glug of vinegar...
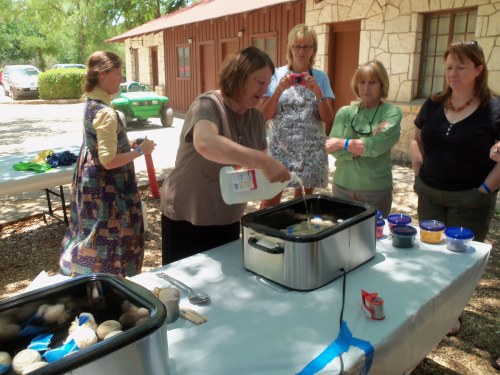
and she's ready to start adding the dye.
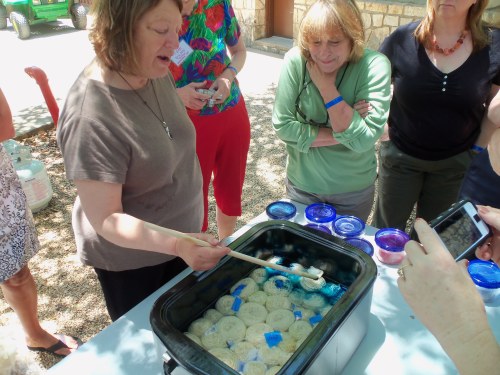
OCD me has always thought that dyeing was something so precise. So it was amazing to watch Judith dip a wet stick into the dye, then dab it onto the fiber. First the primes...
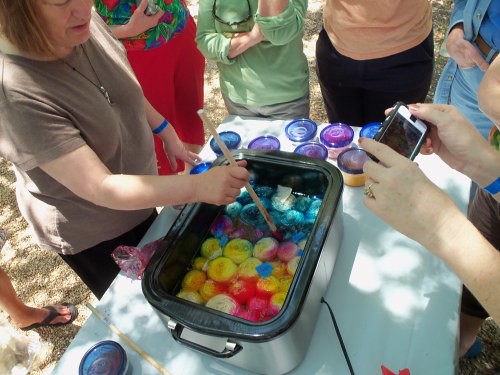
then she started to add the modifiers.
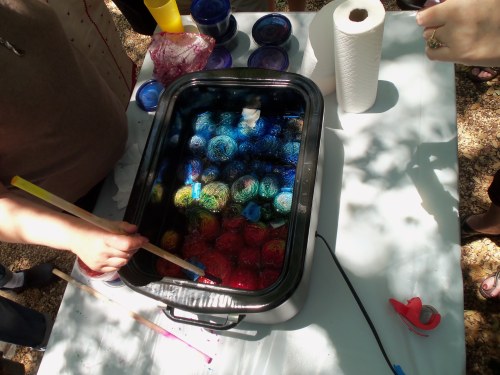
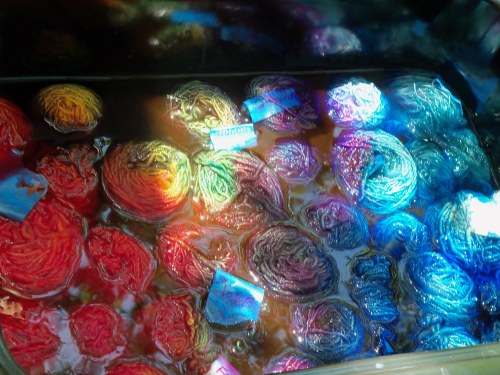
We watched, fascinated with the way each color morphed into another. When the first batch of balls emerged from the dye pot they were each uniquely beautiful.
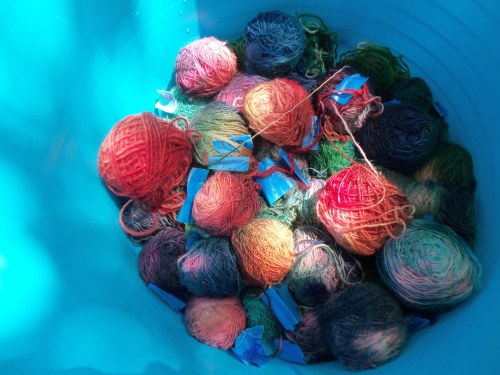
Here are my three.
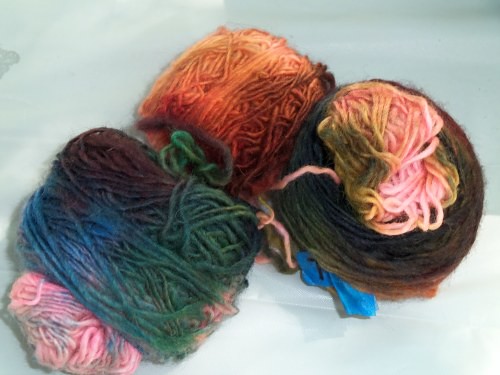
Roddie's and my skeins hanging in the tree to dry...
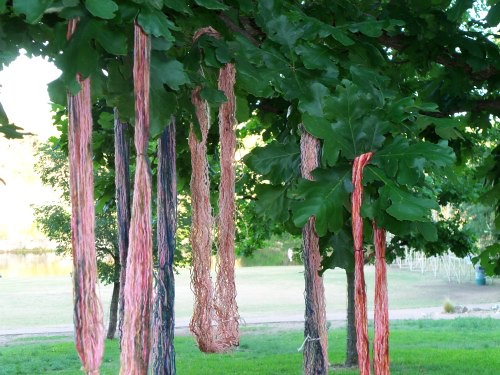
We used these balls to make "art yarn" with slubs, coils, and turkish knots. This was really fun to spin, but I have no idea what to do with the yarn other than a scarf or maybe the base for a necklace. It is pretty though.
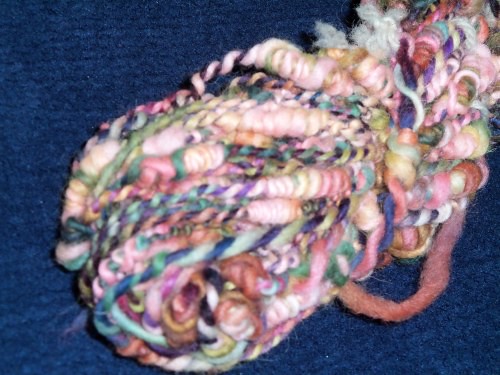
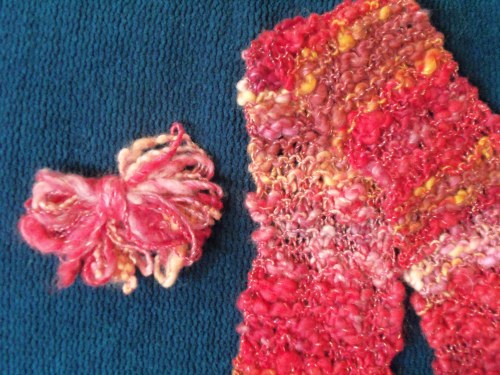
I saved one ball back for the indigo pot on Saturday.
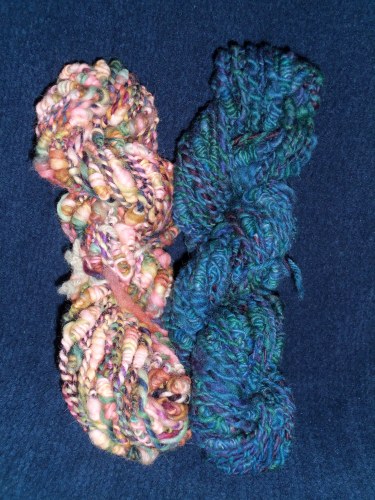
__________________________________________________________
In the midst of everything we had going on, Judith showed us how to make art batts on the big drum carder. We were all mesmerized watching the colors of merino being layered with bits of silk, mohair, and other materials.
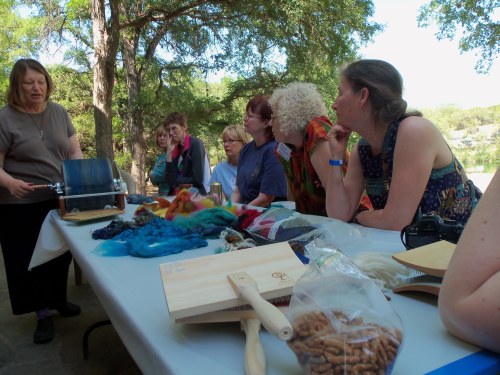
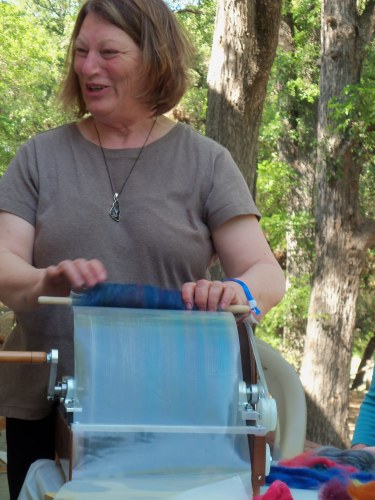
Over the next two days, the basket by the carder would be stocked with lots of fun bits to play with.
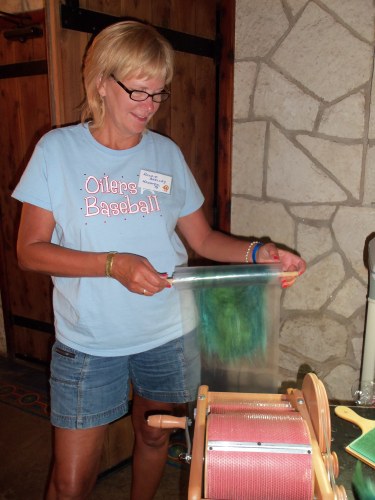
Once we got comfortable using the drum carders, we started a little color study. We each chose one color, then blended it with white, gray, brown, and black. Next we were supposed to spin little samples showing the effects of combining them. That's still on my to-do list, but here's a shot of my yellow, and Roddie's blue.
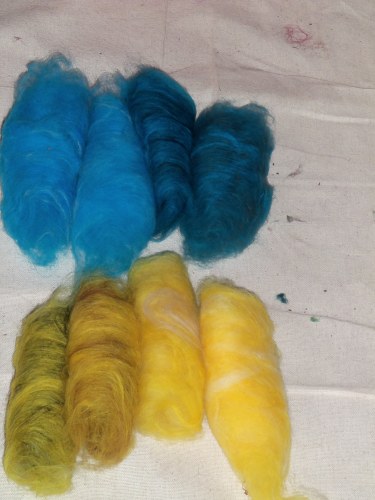
However our overachiever, and amazingly fast spinner, Alecia, not only got hers done, but labled them for the rest of us to use as an example.

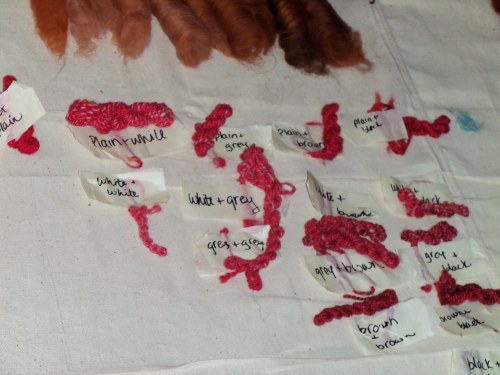
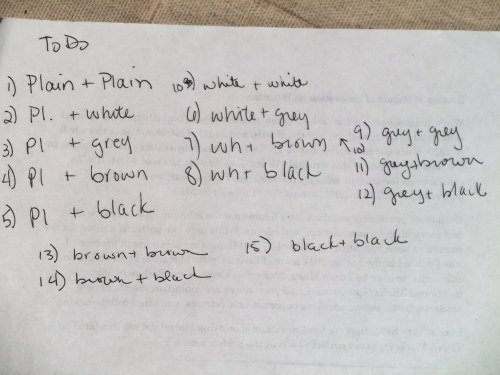
________________________________________________________
Seems like an indigo vat just makes everyone crazy, or maybe it was the margaritas. But on Saturday afternoon, we were dyeing everything we could get our hands on. As fast as Judith could add indigo to the pot, new items appeared to be dyed. People were even dyeing their hair!
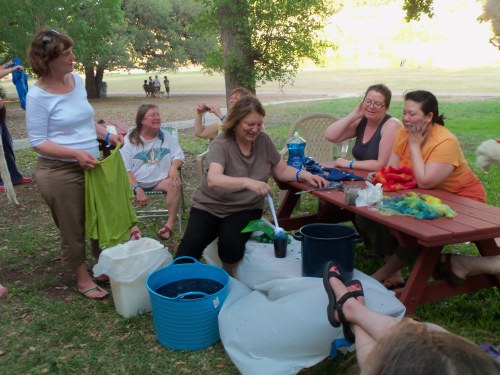
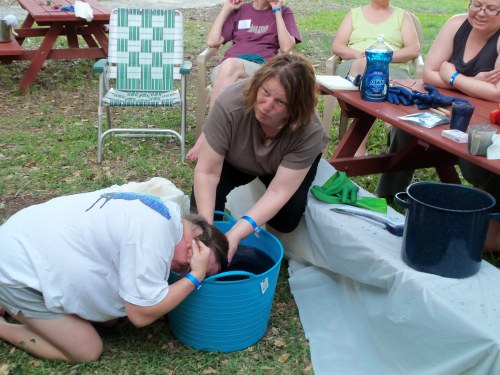
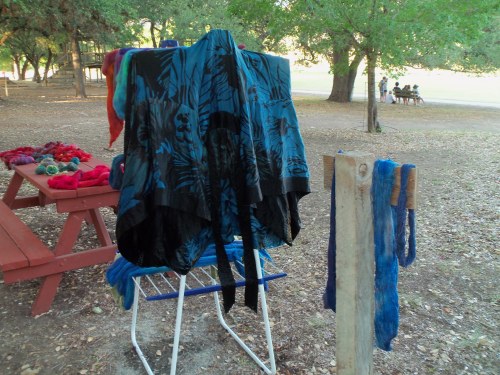
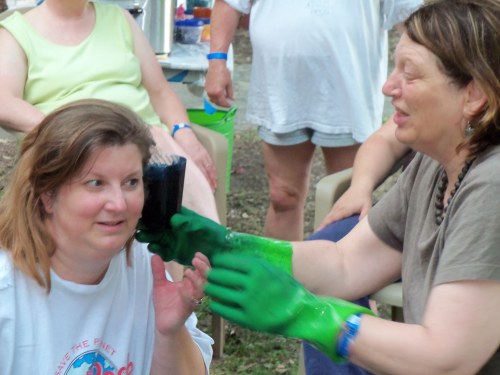
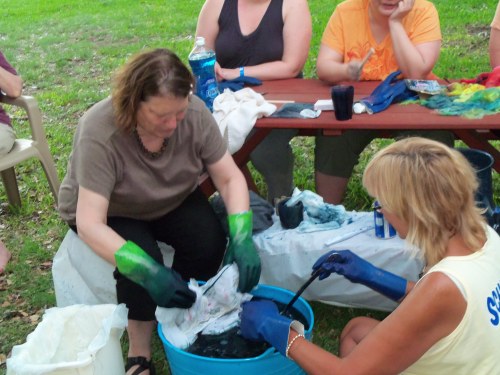
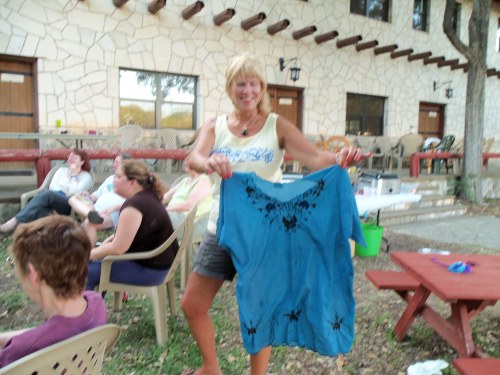
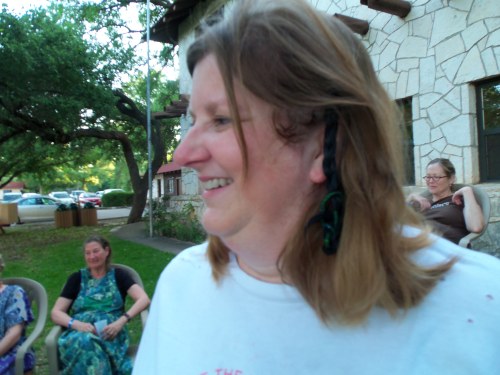

Soon, day turned to night and there were into clothes spread across the lawn and skeins of indigo yarn draped in the trees.
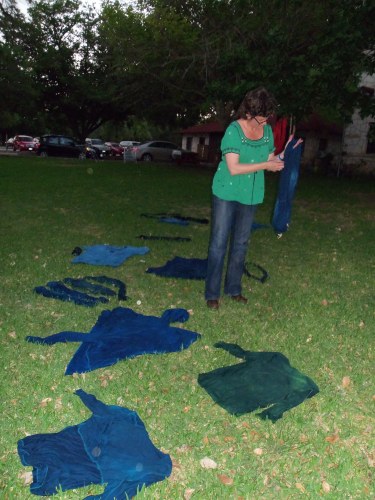
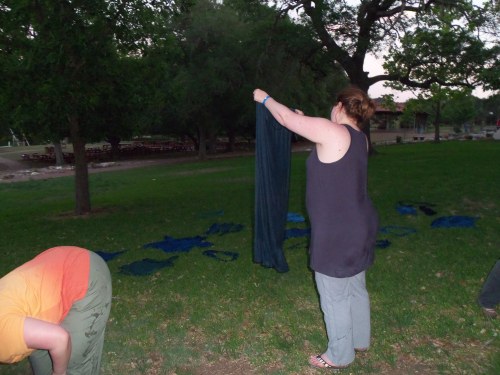
Sunday would arrive too soon, and it was time to say goodbye to new friends.
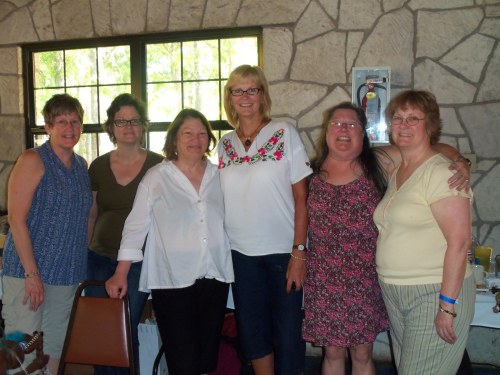
Judging by all the activity on our Ravelry group, everyone came away with a mind full of possibilities and the skills to make them happen. We're already looking forward to next year! Thanks so much Karen for all your hard work putting this together. And a special thank you to Judith for being the open and sharing person that you are. It was an amazing week!